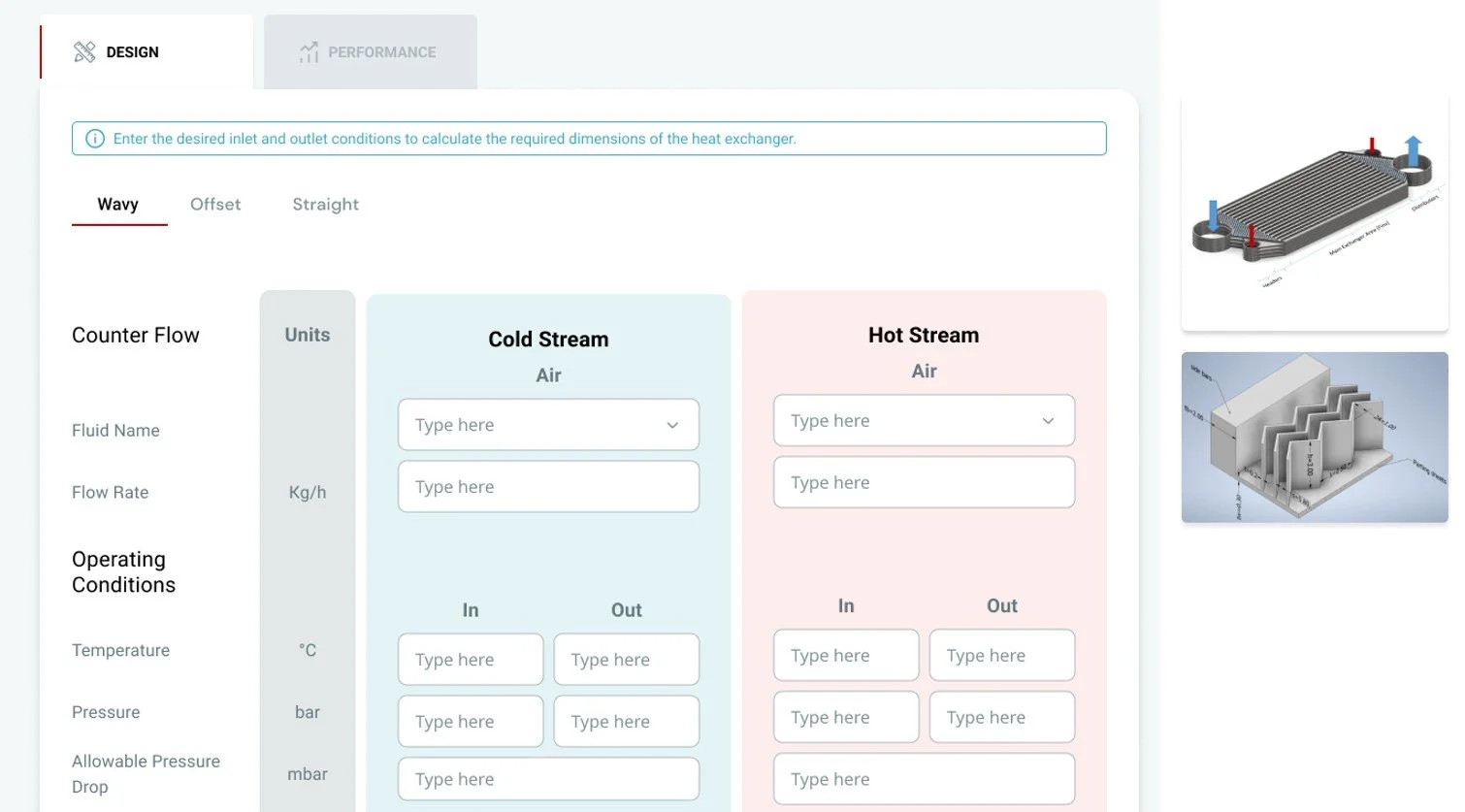
HEAX Overview
Rate, simulate, and design heat transfer equipment
High costs associated with major tube heat exchanger calculation software often place them out of reach for many companies. This is particularly challenging for those that only require occasional calculations throughout the year.
Independence in this context is vital as it empowers companies to perform calculations as needed, without the financial and time constraints of hiring consulting firms. Managing calculations internally not only saves money but also allows for greater flexibility and control over project timelines and budgets. This approach fosters autonomy and cost-efficiency, ensuring that resources are allocated more effectively.
What is HEAX?
HEAX is a state-of-the-art thermal process design and simulation software, engineered to rate, simulate, and design a wide variety of heat transfer equipment. Our calculation methods are built on the latest research and industry data, ensuring accuracy and efficiency. Regular updates ensure that Xchanger Suite evolves to meet your ever-changing engineering needs, providing you with the most advanced tools for thermal process design.
1. Select the Heat Exchanger Type
Begin by choosing the type of heat exchanger you’re working with—whether it’s a shell-and-tube, plate, or finned-tube exchanger. Our software supports a variety of types to ensure your specific needs are met.
Plate and Fins heat
Tube and Fins
Shell &Tubes
Tube Bundle and Fins
Tube bundle
3. Transfer Methods
Transfer Method: Choose between single-phase heat transfer or phase-change processes (evaporation/condensation) depending on the application's requirements.
Wide Range of Fluids: Select from a variety of working fluids, typically the one available in CoolProp library
3. Operating Conditions
After selecting the calculation mode, customize your heat exchanger by choosing features like fin type and inputting operating conditions such as flow rates, pressures, and temperatures
4. Generate Results
Once all details are entered, the software will generate the results, including:
Heat Transfer Rate
Outlet Temperatures
Pressure Drops
Required Surface Area
Coil heat Exchangers
Continous Tube bundle
Microchannels and Fins
2. Choose the Calculation Mode
Select the calculation mode that suits your project:
Design Mode: Enter your desired inlet and outlet conditions (such as temperature and pressure) to calculate the required dimensions and specifications of the heat exchanger.
Performance Mode: Provide the inlet conditions and the existing dimensions of your heat exchanger to determine the outlet temperature and pressure drop.